Why should companies invest in air quality?
- Stricter legal regulations are coming
- The employer's duty of care must be fulfilled
- An attractive workplace is more than just a good salary
- Less fine dust in the air improves the running times of machines, reduces cleaning and maintenance costs
Interview: Less particulate matter, fewer harmful gases: it's possible!
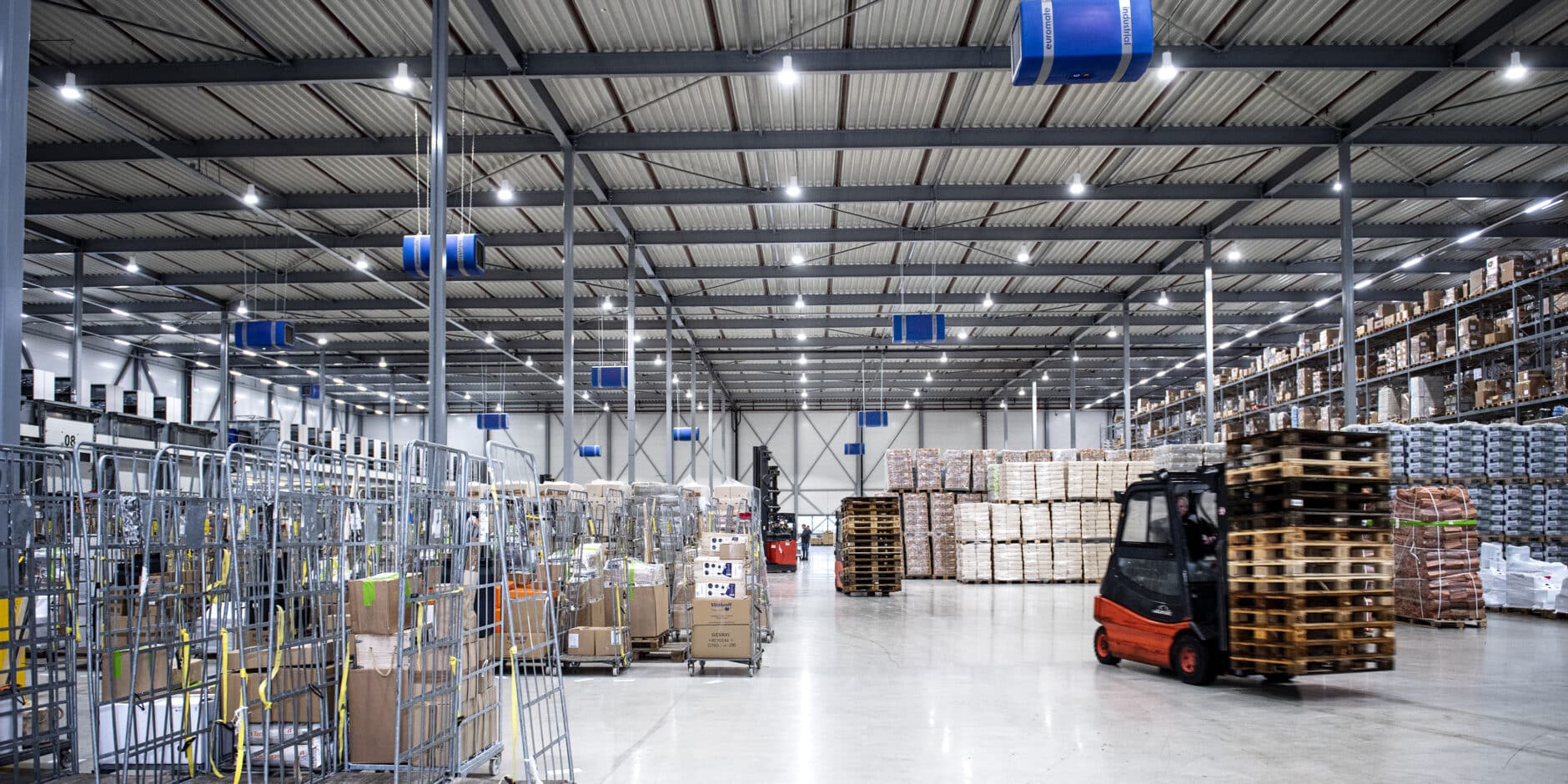
‘Good indoor air quality leads to a healthier working environment, less absenteeism, fewer machine breakdowns and lower cleaning and energy costs.’
This is how Carolien Klees quotes Daniel Gooijer, Managing Director of air quality expert Euromate, in a two-page specialist article in the Dutch magazine ‘Warehouse & Logistiek’ (Warehouse and Logistics) and his plea for greater awareness of particulate matter and its health risks, specifically in warehouses and logistics halls.
The lesser-known topic of harmful gas emissions (formaldehyde, ethylene oxide), which is particularly relevant in warehousing and logistics, is also part of her detailed article, for which she conducted a long expert interview with Daniel Gooijer, excerpts of which are published here with the publisher’s permission.
Particulate matter and logistics – how do they go together?
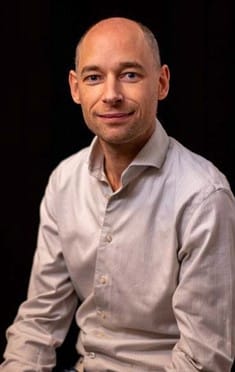
Daniel Gooijer
The fact that particulate matter occurs on motorways or main roads and must be reduced no longer needs to be emphasised or discussed. The wood and paper industry is also still quite well associated with the particulate matter problem, as are open fires and wood-burning stoves. But warehouses and logistics? The topic is not mentioned in the usual portals and specialist magazines, and a Google search quickly leads to logistics as a cause of particulate matter in freight transport.
‘Word has got around that particulate matter is not healthy for humans. However, the fact that a lot of particulate matter swirls around, especially in logistics processes, is rarely discussed. This is not healthy for the people who work there,’ reads an article from 2022 on Aftermarket-Trends. And further:
“In order to comply with regulations, new buildings must fulfil standards such as compliance with new primary energy requirements and improved insulation. Added to this are additional and faster-paced work processes – such as returns, small-quantity shipping and next-day delivery, which ultimately cause more pollution. The increase in online shipping accelerated by the pandemic has intensified these processes. To increase productivity, new packaging machines are being used to tear and cut boxes, enabling more efficient work – but causing more air pollution. This is because the cardboard particles that initially fall to the floor are repeatedly stirred up and dispersed into the air.”
This is precisely where Daniel Gooijer comes in: “Warehouses generate an excessive amount of fine dust, for example when repacking, shredding cardboard boxes, packing goods and cutting and folding cardboard boxes. Fine dust is also introduced through open doors and ventilation systems. Abrasion from floors and forklift tyres also contributes to the spread. The goods themselves can also be a source of particulate matter.
Among other things, fine dust can lead to lung diseases such as COPD and cardiovascular diseases. It also affects machines, production lines and loading conveyors, disrupts work processes and leads to unnecessary downtime. Customers have noticed, for example, that appliances with sensors last much longer if the air is filtered correctly. And cleaning costs are significantly reduced. Today, there are affordable measuring devices that provide an insight into the air quality. This allows potential risks to be recognised immediately and targeted measures to be taken.”
Harmful gases
“The presence of harmful gases can not only jeopardise the health of workers, but can also affect the quality of stored products. Formaldehyde, for example, is a chemical commonly used in adhesives, chipboard and other building materials. With prolonged exposure, it can cause respiratory irritation and even cancer. Another example is ethylene oxide, which is used as a fumigant in certain agricultural products and as a sterilising agent for medical devices and consumables and can lead to stomach problems and most likely cancer if inhaled,” the author continues.
In fact, Euromate offers device/filter combinations that extract harmful gases before they harm people and complicate working conditions.
Is air quality in the workplace regulated by law?
In the interview, Daniel Gooijers also goes into more detail about whether and, if so, how the issue of air quality in the workplace is regulated by law. Is it, one would think, as much as is talked and written about the dangers of particulate matter and other air pollution? However, the sobering answer is that when it comes to limit values, as was the case just a few weeks ago in connection with the EU’s decision to adjust the pollutant limit values to the recommendations of the World Health Organisation, the focus is almost always on outdoor air.
‘In terms of ventilation, the Dutch building regulations stipulate that appropriate ventilation must be guaranteed depending on the number of employees. The requirements are clear and easy to fulfil,’ says Gooijer. ‘However, the utilisation of a room is not taken into account. Packing goods in cardboard boxes, for example, releases large quantities of fine dust, which can create an unhealthy situation despite the prescribed air supply.
There is still hardly any legislation, with the exception of wood dust and other hazardous substances. However, employers have a duty of care. In an existing employment relationship, employers are obliged to support their employees and protect them from hazards. So if they expect a lot of fine dust, they must take measures to protect the health and well-being of their employees.”
“Fortunately,” says Gooijer, “awareness of air quality is growing and the EU will adjust its limit values by 2030, starting with outdoor air. So it’s definitely worth investing in air quality now. And because the solutions offered by Euromate are scalable systems, you can start small and expand the number of devices as the laws become stricter.”
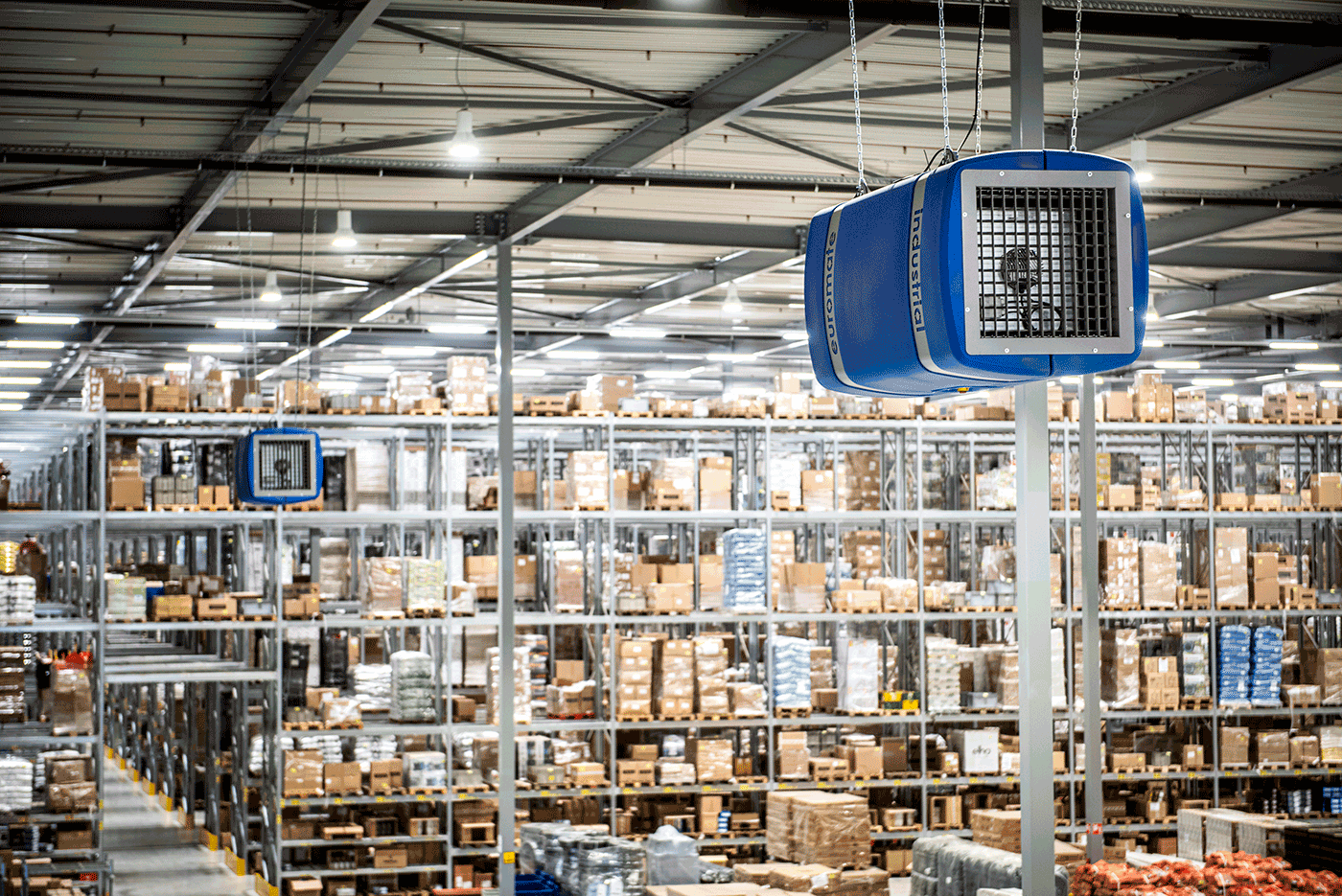
Air filtration at Dutch logistics company Welkoop
Fifty years of experience pay off
Daniel Gooijers summarises:
“Euromate has half a century of experience in analysing and improving air quality. The company offers accessible measurement solutions that enable customers to easily understand air quality via a user-friendly customer portal. The measurement results can be called up at any time and notifications can be set if predefined limit values are exceeded. Based on these findings, Euromate supplies a wide range of air filtration systems for particles, gases, pathogens, oil mist, cooling lubricant mist, welding fumes and grease.
Euromate is an air quality company with its own research and development and service team. The devices are developed, assembled and serviced in-house, which guarantees a long service life.
As a flexible company with short communication channels, Euromate is able to act quickly and also handle larger projects that require extensive project management. For example, Euromate was authorised to install 150 air filtration systems at CEVA Logistics, formerly TNT Logistics, which remove harmful ethylene oxide.
And a pilot project is currently underway at a large retail chain that hopes to retain its employees for longer by improving air quality.”